|
|
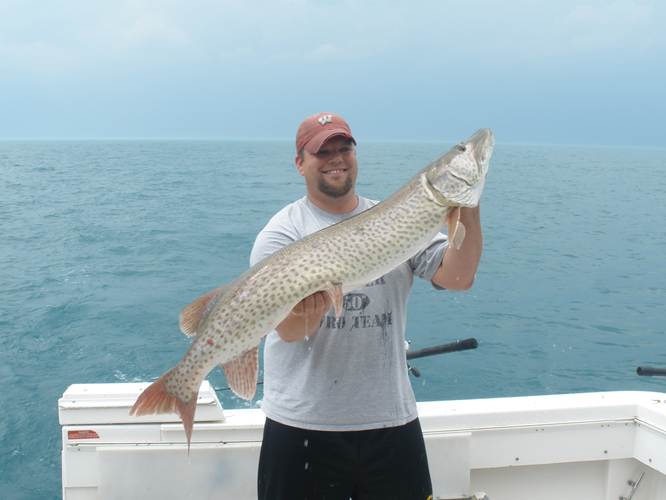
Posts: 774
Location: South East Wisconsin | Question for the guys that make their own globes? If you do thru-wire on a wood lathe, is there one drill bit that out performs the others? I’m having some problems with the bit walking, (wondering) with cedar. Do I want to go fast or slow? Or is there other ways to make your center hole before you turn the bait? Any help would be appreciated. I’m just starting out. | |
| |
Posts: 107
Location: Ohio | Hi,
For my thru-wire, I don't actually drill a hole, I bore it with a steel rod. I sharpen the end to a point and then put grooves in the rod. I do this for my crankbaits made out of basswood and cedar. This works for me with baits up to 8".
Thanks, | |
| |
Posts: 41
| Lots of different ways to skin a cat. I had the same trouble when I first started making lures, boring through the blank for through wire construction and having the bit walk. Ruined plenty of blanks. The trick is in the bit. Most have a pointed cutting tip and as we all know this tends to follow the grain in wood and go where you don't want it to.
I am a blacksmith and it was another blacksmith that turned me on to this tip. He makes guns, specifically American longrifles or "Kentucky" rifles as they are known. They need a long hole drilled in the stock for the ramrod and a V shaped bit is used so the drill runs true through that hard maple and walnut. A standard drill bit is used, brazed to a rod to give whatever length you want, a foot long or 6 feet, whatever you need. You might have to do this if you can't find foot long bits at a wood worker's supply or you just want a longer length.
(wear safety glasses for all of this)
For the bit I recommend you soften it by annealing before redressing the shape of the tip. Annealing it makes it a whole lot nicer to work with and sharpen now and then with just a few file strokes.
You don't need a forge to heat the bit, just use a mapp torch or a butane torch.
You need a bucket half full of dry sand, and more to dump on top later.
Grip the bit at the tail end in vice grips and then put the vice grips in a bench vice. Heat the bit an even bright red all over. Keep it in the blue flame and wave the flame up and down the full length of the bit so it takes heat evenly. If you get it past a red heat into yellow and you see sparks discard that bit and start over with a new one. There is no saving it, once you have a 4th of July sparkler it is toast so just throw it away. Once you have a nice bright red all over, not a dull blood red, take the vice grips out of the bench vice (a glove is nice to have on your hand here) and carefully release the bit onto the sand in the bucket. Now fill up the rest of the bucket with more sand so the bit is buried in the middle. Leave it until tomorrow. Now it is annealed (softened) and will be easier to work.
DO NOT quench it in water once you have it red hot, this makes it not only harder but also brittle like glass. Being put into the sand red hot and cooling slowly over hours is what softens it.
Now you have a soft bit. Grind or file the tip down flat. I recommend filing but if you use a bench grinder dip it in water to keep it cool -A LOT- just a second or two on the wheel and then cool it again. If you see colors appearing like black or "pigeon blue" you have imparted an uneven temper and might as well start over because it will be prone to chip under use.
Once you have the tip flat you can begin to make it into a V. The best way is to start with a cut made with a fine hobby saw that will cut metal (mini hack saw). Just make a shallow cut right into the center, it's best to use all draw strokes (towards you), only takes a few to get a slot started. This serves as a guide for a triangle file to make the V. That's it. The edges should be sharp enough to cut cedar just fine at this point.
I use a post drill for drilling the through wire holes in my blanks. This is a hand operated antique that gives total control over speed and has a ratcheting feed that is also hand adjustable. Mine is a Champion model 101, It looks like this-
http://www.google.com/imgres?imgurl=http://homepage.mac.com/galoot_...
You don't have to have a hundred year old blacksmith's drill but it sure is nice to have and they're not all that hard to find at farm auctions or on Epay. They go for about $150, anything higher is too much and they're trying to scalp you, trust me they go for a buck and a half and aren't to tough to find. The reason I say this is because outside of blacksmithing circles these tools can be a bit hard to find and antique dealers think they're made of gold. Go to www.abana.org and click on "affiliates", a scroll down list appears showing contact information for blacksmithing groups all over the country, these guys can find you a post drill at a fair price if you really want one.
Edited by Lunge Master 2/13/2011 10:37 PM
| |
| |
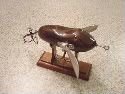
Posts: 910
Location: Hastings, mn, 55033 | Lunge,
What would you charge to make a fella a couple of those bits, maybe a 1/8"x6" and 1/8"x8" and a 1/8"x10" bit. | |
| |
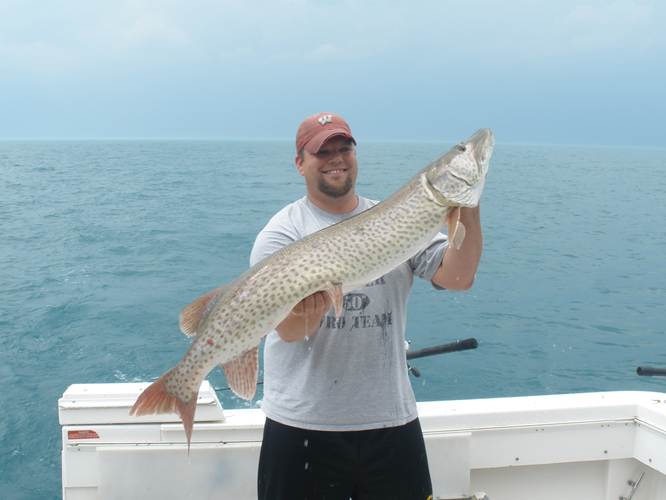
Posts: 774
Location: South East Wisconsin | Good information Dan, I would be interested as well. Could you use those bits on a wood lathe with a chuck adapter? My lathe has pulley speeds and I don’t think I can get down slow enough. I’m on the second to last wheel and she’s moving pretty quick. | |
| |
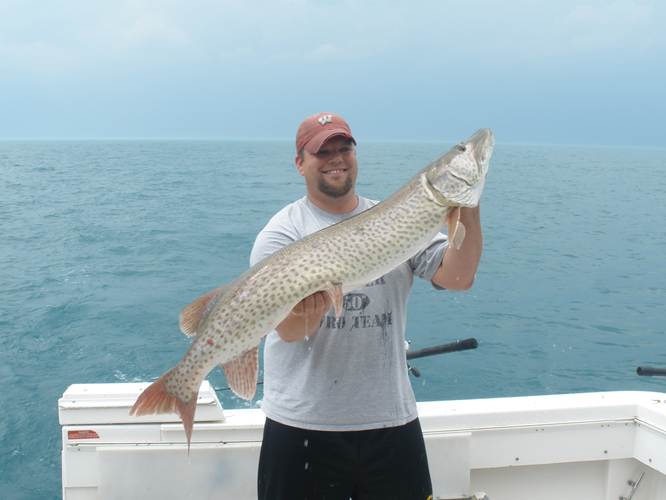
Posts: 774
Location: South East Wisconsin | Dan, do they look like this?
Attachments ----------------
Vshape.jpg (31KB - 156 downloads)
| |
| |
Posts: 41
| I could sell you a few but for the same money you could gather the few tools, a torch and some jeweler's files and just do them yourself, then you can do them whenever you need more. As far as length goes, 12" long bits are available as are 8" and 6". You that should suffice for anything up to a 10" lure blank. If you do want bigger then you'll have to go with the rod extension method, your local welding shop can hook you up by mig welding them for you. Make sure the rod you use matches the diameter of the bit. You could make the jig for them easily enough to take with you right at home with just a few simple hand tools, a cordless drill and a file. It's just a piece of angle iron with a slot in the bottom of the angle. Drill a row of 3/8" holes as close together as possible and clean up with a file so you have a 1 inch long slot. With the V of the angle up ( I drilled holes towards the ends and screwed on some 45* wooden "feet" so it stands up) lay the rod and the bit in there so the ends butt up to each other over the slot where they can be brazed or tacked together with a mig welder. Mine is a foot long with the slot in the middle. Hold them in place in the jig with magnets so they don't move and keep their alignment, you should wind up with one long bit that is straight & true. DO NOT quench it in water, let it air cool right in place for a minute before removing the magnets, rotate it in the jig and do the other side of the tack. Chuck it up in a lathe or drill press and run a file against the bulb of the weld to smooth it out. I do this in a bench top drill press, chuck up the bit and then drill down into a piece of scrap wood an inch or so and lock in in place. With the bit running with the end in the wood it stays put and doesn't push away from the file. Just squirt a little cutting oil at it and sort of rub the file around in a circular motion and that bulb vanishes in just a minute. Make the jig which is easy enough at home and if you don't have a mig take it to a welding shop with your bits & rods and all he has to do for you is tack them, it'll cost more for the shop time than the service, half a dozen will run you about $20. I like 1/8" standard bits (not hard carbide metal working bits) and 1/8" welding rod (tig filler rod, not flux coated stick welding rod, or mild steel round stock if you can find 1/8" at your local steel supply. These folks will cut you a 12" piece of 1 1/2" angle so you don't have to buy the standard 8' or 16' length or pay through three times as much for a 48" piece at the Farm & Fleet). I first tried using 3/32" rod and bits because I wanted as small of a hole as possible but I found it difficult to work on such tiny drill bit tips.
As far as using a lathe goes for drilling through wire holes in blanks just use whatever is more comfortable for you, a lathe or a vertical drill press with a vice at the bottom. Remove the table if you have to and rig another further down if you need more space. With the drill press you are limited to the travel of the feed unless you modify it. I like the post drill because it goes as slow as I want it to and with the adjustable feed honestly I could drill through an onion one layer of skin at a time and advance it as quickly or slowly as I need. If I feel it bind I can stop immediately and run it backwards a few revolutions. With power tools you notice a bind when the bit breaks. I have a 48" lathe but even on it's slowest speed I still get walkers which tends to happen more the longer the bit is. If I did not just happen to have a post vice because of another hobby I think I would have powered down my lathe with a smaller motor. Another option is to install a rheostat so you can have total control of the speed. Don't skimp by using a household dimmer switch, go to an electrical supply and get a real rheostat. That might solve all your overspeed problems right there.
You don't really have to go through the trouble of annealing your bits, it just makes them easier to file and if you're drilling only soft wood they don't have to be hard anyway. You may find, depending on the type of wood you are using that a V is not best. A "uu"shape may work better, the V will work, just takes longer and stays true better. For the uu start the same way by filing the tip flat and then take a round file and hold it at a 45* and sharpen the flutes on each side. this leaves a little raised tip in the center but will not walk like a pointed tip does which tends to follow the grain.
Get a quality set of jeweler's files, not the cheap crappola at Harbor Freight made by Hong of Kong, they are worthless.
Edited by Lunge Master 2/14/2011 1:01 PM
| |
|
|